JSEDM ZNC EDM: High-Performance Electrical Discharge Machines for Precision Mold Processing
JSEDM's ZNC Electrical Discharge Machines deliver precise mold processing with low operating costs. Our user-friendly EDM systems feature numerically controlled Z-axis function, stable operation, and easy maintenance, perfect for plastic injection molds and small batch production. Discover Taiwan's leading EDM technology with 40+ years of expertise.
ZNC EDM
Also known as an electrical spark machine, can use copper or graphite as electrode to process various conductive materials. It is mostly used for processing plastic injection molds
A ZNC electrical discharge machine is a specialized tool used for electrical discharge machining, primarily for precision and complex mold processing in manufacturing. Its working principle involves using electrical sparks to remove material from the workpiece, achieving the desired shape, size, and surface finish. This method is particularly suitable for hard, conductive materials such as steel, aluminum, and copper.
The main feature of a ZNC electrical discharge machine is its numerically controlled Z-axis function. By precisely controlling the discharge current, discharge time, and discharge frequency, it can achieve accurate machining of workpieces. The ZNC electrical discharge machine uses manual control or a simple numerical controller (NC) to adjust the discharge depth and position. Its characteristics offer several specific advantages:
- Low Cost: Due to its relatively simple control system, the purchase and maintenance costs of a ZNC electrical discharge machine are typically lower, making it a choice for manufacturers with limited budgets.
- Easy Operation: The interface of the ZNC electrical discharge machine is relatively intuitive, with a gentle learning curve for operators without highly specialized knowledge. Its manual control function allows operators to make adjustments more flexibly.
- Suitable for Small Batch Production: Due to its simplicity and low cost, the ZNC electrical discharge machine is particularly suitable for small batch production and customized production needs, giving it unique application value in certain production environments.
- Easy Maintenance: Due to its simple structure, the ZNC electrical discharge machine is relatively easy to maintain, reducing production line downtime and repair costs.
- Strong Adaptability: Although the ZNC electrical discharge machine has simpler controls, it still has enough adaptability to meet various workpiece processing needs, especially for more basic and standard machining tasks.
- Stable Operation: Due to the relatively simple control system of the ZNC electrical discharge machine, its operational stability and reliability are relatively high, which helps ensure machining quality and production efficiency.
Working Principle of ZNC Electrical Discharge Machine:
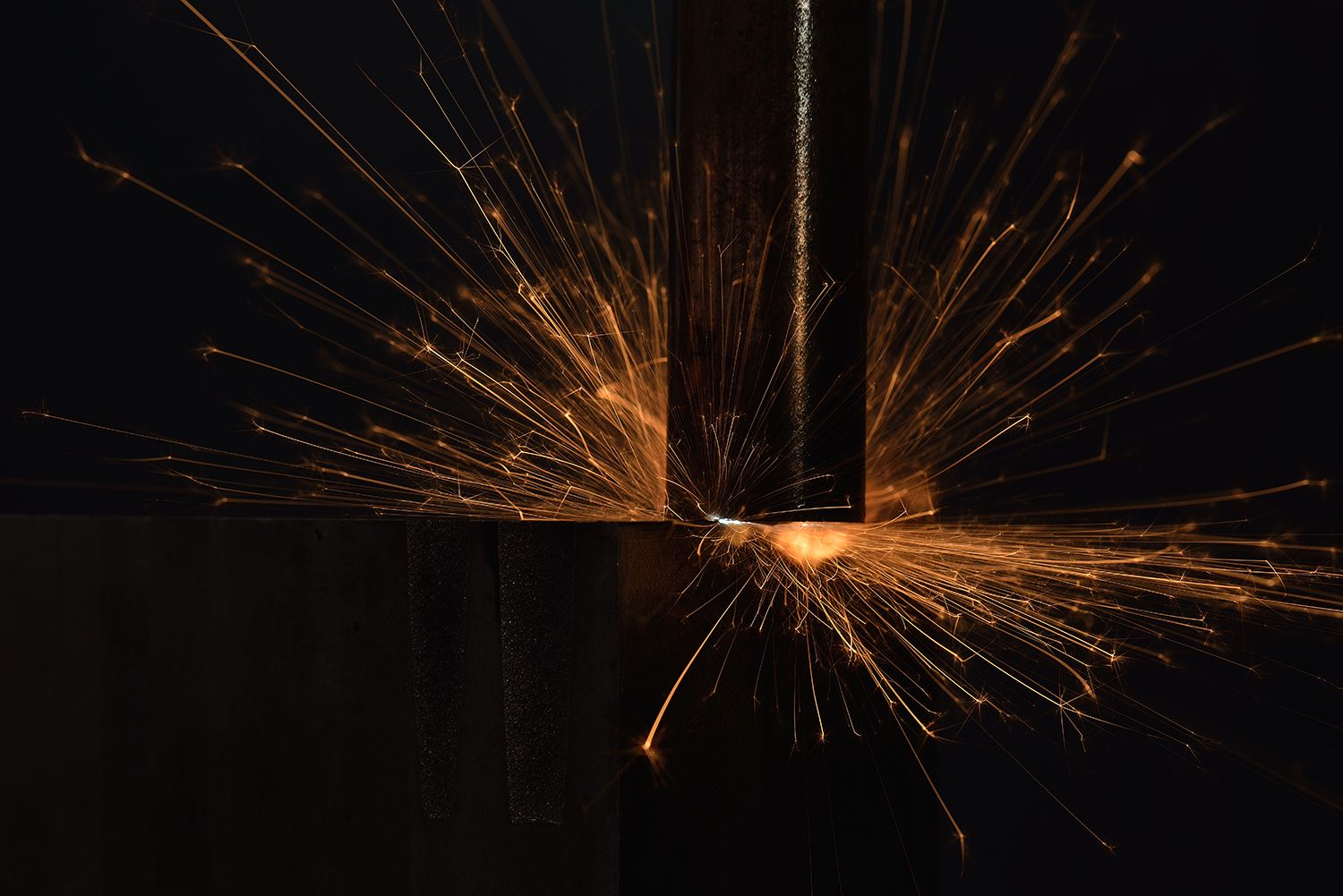
Electrical discharge machining is a non-traditional material removal process. During the discharge process, the gap between the electrode and the workpiece is filled with an electrolyte. When they come close to each other, the voltage causes the electrolyte in the gap to generate electrical sparks. These sparks heat and melt the material on the surface of the workpiece, causing it to be removed.
How Can ZNC EDM Technology Reduce Your Mold Production Costs While Maintaining Precision?
JSEDM's ZNC EDM machines deliver exceptional cost efficiency for mold manufacturers through simplified controls and reduced maintenance requirements. Unlike more complex systems, our ZNC technology offers the precision you need for plastic injection molds at a fraction of the investment, with intuitive operation that minimizes training time and maximizes productivity. Contact us to discover how our customers typically achieve 30% lower operational costs while maintaining the exacting standards their projects demand.
Designed with both performance and practicality in mind, our ZNC EDM machines feature intuitive controls that reduce operator learning curves while maintaining the precision Taiwan's manufacturing is known for. The system's ability to process various conductive materials using copper or graphite electrodes provides versatility across multiple applications, while the stable operation and low maintenance requirements minimize production downtime. With over 40 years of EDM manufacturing expertise, JSEDM delivers these cost-effective solutions without compromising on the quality and reliability that have made us a trusted global supplier in the metalworking machinery industry.